Turbocharger bearing lubrication system
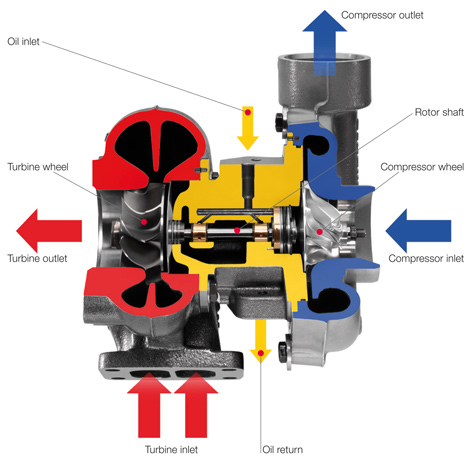
Turbocharger bearing lubrication system
– Bearings are either of the ball or roller type or plain white metal journals.
– The ball and roller bearings are mounted in resilient mountings incorporating spring damping to prevent damage due to vibration. These bearings have their own integral oil pumps and oil supply, and have a limited life (8000 hrs).
– Plain journal bearings are lubricated from the main engine oil supply or from a separate system incorporating drain tank, cooler and pumps. Oil is supplied in sufficient quantity to cool as well as lubricate.
– The system may incorporate a header tank arrangement to supply oil to the bearings whilst the turbocharger comes to rest should the oil supply fail. A thrust arrangement is required to locate and hold the rotor axially in the casing. In normal operation the thrust is towards the compressor end.
Double row ball bearing
– Turbocharger blower side double row ball bearing arrangement that is commonly provided. The inner race of the bearing is a tight fit on the shaft. Between the outer race and the bearing housing leaf spring are fitted both axially and longitudinally as shown.
– Leaf springs served to damper vibration and reduce chattering of the steel balls or rollers, thus prolonging the useful service life of the bearing.
– The bearing is completely enclosed in casing and bottom part of the casing forms lubricating oil sump. A gear type pump driven by the turbine shaft draws oil from the sump and supplies a jet of oil to the bearings.
– A sight glass for checking oil levels and oil filling and drain plug are provided in the casing. The blower side bearing also serves to locate the T/C rotor assembly in the axial direction and absorbs any axial thrust.
– The turbine side bearing and lubrication arrangement are similar except that this bearing is of single row type and the arrangement allows thermal expansion of the rotor shaft.
– This type of lubrication system is employed in axial T/C where the bearing support is at the end and the rotors are in the centre.
– This arrangement contains self-contained gear type pump operated by the turbine shaft, It draws oil from an independent bearing sump and supplies at pressure to the bearings.
– Bearings used may be ball or roller bearings.
Advantages
– Since the pumps are at the end of the shaft, inspection and maintenance is easy.
– Independent sump, no additional fittings such as cooler, filters is required.
– A choice of lubricating oil or turbine oil is available.
– Initial cost is also low.
– Better lubrication with increase in speed.
– Reduction in frictional losses at high speed.
Dis-Advantage
– Poor lubrication at starting and at low speeds.
– Static brinelling can occur due to rubbing of bearings caused by vibrations (in the absence of oil)
– Oil needs to be renewed at regular intervals.
– Finite life of the pump.
– Different grade of LO other than system oil will incur additional cost.
– Failure of attached pump will cause heavy damage to T/C.
Gravity type lubrication
Journal sleeve type bearing
– The sketch shows journal sleeve type bearing arrangement. Also shows, diagrammatically the arrangement of blowers and turbine rotor, bearing labyrinth seal, air filter and ducting of a radial flow the bearing are lubricated either by oil supplied under pressure by a pump or by gravity form a header tank which is continuously replenished by a pump.
– This type of lubrication employed in radial T/C.
– The bearing support is at the centre and compressor and turbine wheels at the end.
– Sleeve type of bearing is used in this arrangement with lubrication from engine lube oil system.
– L.O supply is available as long as the main lubricating oil pump is working i.e independent of T/C working or standstill.
– A non-return valve with a orifice is provided in the supply line which allows oil to pass to the header tank.
– In-case of failure or accidental stoppage of main L.O pump, if the T/C still running, oil is supplied from the header tank.
Advantages:
– Continuous lubrication is available
– Separate oil is not required, system oil can be used.
– Less chances of static brinelling between shaft & bush/sleeve. Due to presence of LO film.
– In case of failure of main pump, backup from header tank is available.
– L.O need not be changed or renewed at regular intervals.
– Lubrication is efficient for all range of speeds.
Disadvantages
– Initial cost is very high due to piping, coolers, filters and header tanks requirement.
– Elements in the piping might get carried away and cause damage to bearings.
– Deterioration in quality of system L.O will damage the bearings.