Electronic soft starting of large marine motors
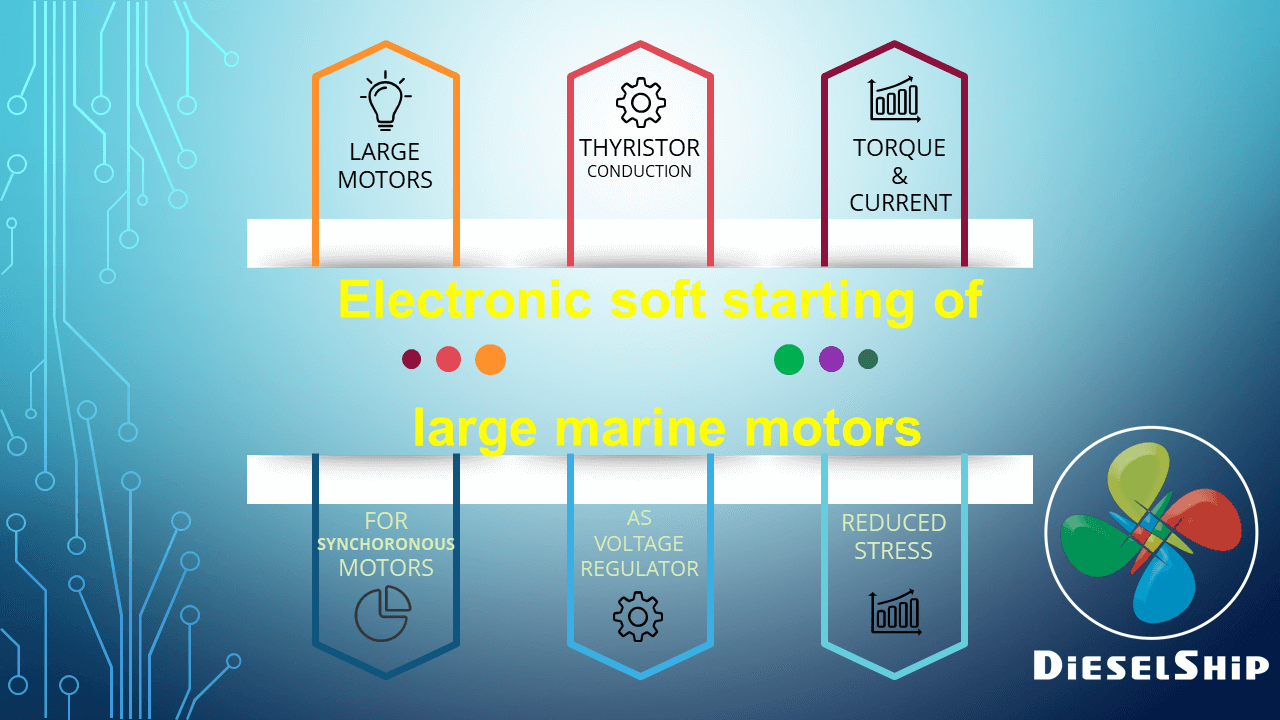
Electronic soft starting of large marine motors
- A motor soft starter is a device used with AC electrical motors to temporarily reduce the load and torque in the power train and electric current surge of the motor during start-up. This reduces the mechanical stress on the motor and shaft, as well as the electrodynamic stresses on the attached power cables and electrical distribution network, extending the lifespan of the system.
- It can consist of mechanical or electrical devices, or a combination of both. Mechanical soft starters include clutches and several types of couplings using a fluid, magnetic forces, or steel shot to transmit torque, similar to other forms of torque limiter. Electrical soft starters can be any control system that reduces the torque by temporarily reducing the voltage or current input, or a device that temporarily alters how the motor is connected in the electric circuit.
Which of the motors in ship require soft starting
- Starting of induction motors is accompanied by inrush currents up to 7-10 times higher than running current, and starting torque up to 3 times higher than running torque. The increased torque results in sudden mechanical stress on the machine which leads to a reduced service life. Moreover, the high inrush current stresses the power supply, which may lead to voltage dips. As a result, lifespan of sensitive equipment may be reduced.
- A soft starter eliminates the undesired side effects. Several types based on control of the supply voltage or mechanical devices such as slip clutches were developed. The list provides an overview of the various electric start-up types. The current and torque characteristic curves show the behavior of the respective starter solution. Torque surges entail high mechanical stress on the machine, which results in higher service costs and increased wear. High currents and current peaks lead to high fixed costs charged by the power supply companies (peak current calculation) and to increased mains and generator loads.
Working of soft starters
- The idea behind a soft start is to gradually allow the motor current to rise until the motor reaches its steady state. This reduces start-up current but also reduces start-up motor torque. Soft starters adjust motor voltage through use of back-to-back thyristors or triacs in each ac supply line to the motor.
- The thyristors are actuated during the start-up phase such that their turn-on is successively delayed less for each ac half cycle. The delayed switching effectively ramps up the average ac voltage to the motor until the motor sees full line voltage. Once the motor hits its rated speed, the thyristor switching circuit may be bypassed. Larger motors employ either soft starters or they are controlled by variable-frequency drives that incorporate a softstart function.
Thyristors in a soft starter let part of the voltage through at the beginning of the starting sequence and gradually increase it according to the set ramp time. The thyristors can also typically implement a soft stop by reducing motor voltage according to a set ramp time.
How does star-delta starter compare to a electronic soft starter?
- A special kind of soft-start function called star-delta start is sometimes used on three-phase motors. Basically it starts the motor with stator windings connected in a wye configuration and switches them to a delta configuration when the motor hits its normal operating speed. Here, the starter normally consists of a contactor for each of the three phases, an overload relay and a timer that sets the duration of time in the star-position.
- The starting current is about 30% of that seen during direct on-line start and the starting torque is about 25% of what would be available at a direct on-line start. This starting method only works when there is a light motor load during the start. Shipboard motors that are too heavily loaded like ballast pumps, Combustion fans, Engine room air supply fans, Large AC unit motors, won’t have enough torque to accelerate up to speed before being switched over to the delta position.
Torque & current characteristics as compared to star delta starters
A typical soft starter reduces the motor torque and current during start-up. The star-delta starter accomplishes the same thing but by means of switching motor windings from a star to a delta connection at the appropriate time.
Can electronic soft starter be used in synchronous motor?
- Soft starters are generally used with induction (asynchronous) motors. But they also may provide benefits powering synchronous motors.
- The reason is that many synchronous motors behave like induction motors initially when they start up. That is, there is a lag between the rotating electric field and the rotor position. There is a delay before the motor comes into a synchronous condition.
- As in the case of induction motors, synchronous motors can also draw large stator currents during start-up of perhaps five to eight times the full load current in the absence of soft starting.
soft starters of large marine motors as voltage controllers or voltage regulators
- In both induction and synchronous motors, high stator and rotor current at start-up leads to a low power factor, typically about 0.2 lagging. Power factor and, thus, energy efficiency, rises as the motor accelerates up to its running speed. In this regard, it should also be noted that some soft starters could serve as voltage controllers or voltage regulators for the motor. Their back-to-back thyristors or triacs make this possible because they can adjust motor voltage depending on the load the motor sees, when paired with an appropriate controller.
- Thus, functioning this way, a soft starter can double as an energy manager: A controller monitors the motor power factor, which is a function of motor loading. On light loads, the power factor is low enough that the controller reduces the motor voltage and, thus, the motor current.
Selecting the right Soft starter
- Many of the applications to which soft starters are applied fall into general categories of pumps, compressors, and conveyors. There are a few rules of thumb
for each of these uses. - The start-up time for soft starters is user settable. The typical start-up time for most applications ranges from 5 to 10 sec. The longer time periods tend to be found in pumping and compressor applications where there is a high possibility of pressure waves building up in piping systems.
- The initial start voltage is settable as well, but most applications use a start level that is 30% of the line level. Screw compressors and large incinerator conveyors sometimes start at higher levels (perhaps 40%) depending on the load — conveyors sometimes have material on them when they start up so they may need a higher starting torque, and screw compressors have don’t develop much pressure at low speeds.
Rating of the start starters
- Soft starters typically have the same rating as the motors they power. The situation may be different for start-up ramp times and initial voltage levels that are outside the norm.
- For heavy-duty uses, a common practice is to use a soft starter having a power rating one size bigger than the motor and to use an overload relay when ramp
times grow long; same for applications with frequent starts.
Soft starters in wikipedia
Excellent platform for shipping fraternity to bond and reinforce the shipping industry.
Am looking for a electrical motor soft starter
TYPE: CMS
SUPPLY VOLTAGE: 400
POWER: 37KW
CONTROL VOLTAGE: 240v To be used in a marine boat
Am looking for a electrical motor soft starter. TYPE CMS.. SUPPLY VOLTAGE 400.. POWER 37KW.. CONTROL VOLTAGE 240V