The Accumulation Pressure Test: A Critical Pillar of Boiler Safety and Pressure Management
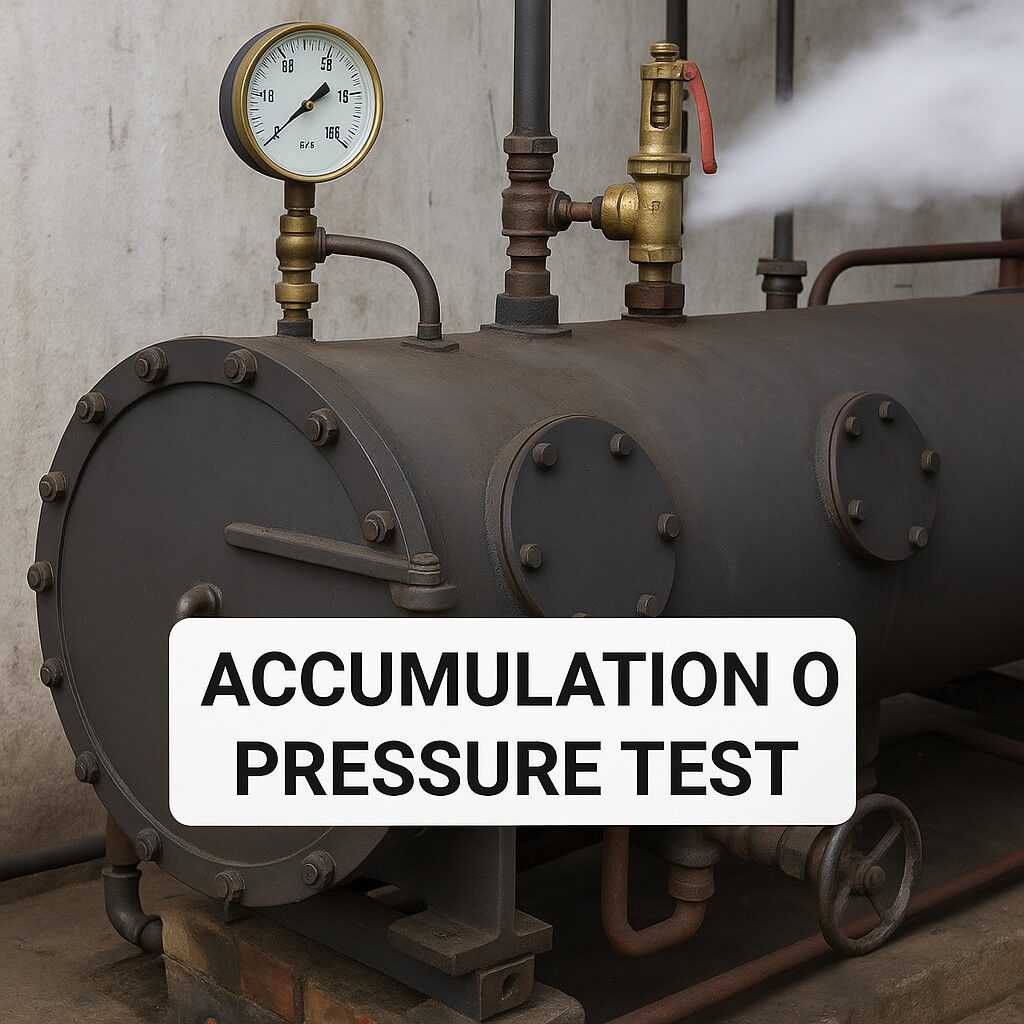
The Accumulation Pressure Test: A Critical Pillar of Boiler Safety and Pressure Management
Executive Summary
The Accumulation Pressure Test (APT) is a specialized, on-boiler procedure fundamentally designed to empirically verify the actual discharge capacity of a boiler’s safety valve system under maximum load conditions. This test is distinct from routine safety valve setting, which focuses on individual valve calibration. The APT’s critical role lies in ensuring that, even under full firing with all steam outlets closed, the boiler’s internal pressure does not exceed a predetermined safe threshold, typically 10% above its design pressure. Adherence to stringent regulatory standards, such as those outlined by the ASME Boiler and Pressure Vessel Code (BPVC) and the Indian Boiler Regulations (IBR) 1950, is paramount. The APT is a high-stakes procedure demanding meticulous planning, precise execution, and rigorous safety protocols to safeguard against catastrophic failures, ensure operational integrity, and maintain regulatory compliance.
1. Introduction to Boiler Pressure Integrity
Overview of Boiler Safety and Pressure Management
Boilers are indispensable assets in a multitude of industrial processes, serving to generate steam or hot water under inherently extreme conditions of pressure and temperature. The immense energy contained within these systems necessitates the implementation of exceptionally stringent safety protocols to avert catastrophic failures. Such failures, particularly boiler explosions, can lead to devastating consequences, including extensive property destruction, severe injuries, and even fatalities.1
Effective pressure management forms the bedrock of boiler safety. This is not a singular action but a multi-faceted approach that encompasses robust design, meticulous operational procedures, and the rigorous, routine testing of all pressure relief mechanisms. The primary line of defense against overpressure conditions is the safety valve system, which is engineered to automatically discharge steam or hot water, thereby preventing internal pressure from exceeding safe design limits.1
The accumulation pressure test, while a specific procedure, is not an isolated step in boiler safety. Its effectiveness is deeply intertwined with the prevention of severe accidents, such as explosions. This procedure is a critical component of a larger, interconnected system of boiler safety. It is an indispensable part of a comprehensive safety strategy, demonstrating that safety is achieved through a synergistic approach involving design, operation, and maintenance. This foundational understanding informs the subsequent discussions on regulatory compliance and best practices, illustrating how individual components and tests contribute to overall system reliability and risk mitigation.
2. Understanding the Accumulation of Pressure Test (APT)
Definition and Core Principles
The Accumulation Pressure Test (APT) is a specialized, on-boiler test specifically designed to empirically verify the actual discharge capacity of a boiler’s safety valve system.3 Its fundamental objective is to confirm that the installed safety valves possess sufficient capacity to release steam at a rate that effectively prevents the boiler’s internal pressure from rising beyond a predetermined safe threshold. This must hold true even when the boiler is operating under its maximum firing conditions with all steam outlets closed.3
The core principle underpinning the APT is the simulation of a “worst-case scenario.” This involves intentionally operating the boiler at its full steam generation capacity while simultaneously preventing any steam from exiting the system through normal operational pathways, such as by closing the main stop valve. This action forces the safety valve(s) to become the sole means of pressure relief, thereby demonstrating their ability to manage the entire boiler’s output.3 The term “accumulation pressure” itself refers to the transient rise in boiler pressure that occurs as a spring-loaded safety valve begins to lift and discharge. This phenomenon is caused by the increased load resulting from the further compression of the valve’s internal spring as it opens.3
The repeated instruction to conduct the APT under “full firing conditions” with the “main stop valve closed” is highly significant. This is not merely a set of arbitrary test parameters; it represents a deliberate engineering and safety philosophy. By simulating the most extreme operational scenario—maximum heat input with no steam demand—the test rigorously challenges the pressure relief system. The 10% accumulation limit further reinforces this by providing a controlled safety buffer beyond the nominal design pressure, acknowledging that even perfectly functioning safety valves will exhibit some degree of overpressure during their full relief cycle. This approach moves beyond theoretical calculations to empirical validation under peak stress, demonstrating a proactive, rather than reactive, risk management strategy. It illustrates that regulatory bodies and industry best practices are designed to test equipment not just for normal operation, but for its absolute limits, thereby minimizing the probability of catastrophic failure in unforeseen or emergency conditions.
Purpose and Significance: Why the APT is Performed
The primary and most critical purpose of the APT is to confirm that the installed safety valves are correctly sized and possess adequate discharge capacity for the specific boiler they are protecting.3 This test is particularly crucial for newly commissioned boilers or when new or overhauled safety valves are installed, ensuring their compatibility and performance with the boiler’s design output.3
The test ensures that, even under the extreme conditions of full firing and with the main steam stop valve closed, the maximum accumulated pressure within the boiler does not exceed a specified safety margin. This margin is universally set at 10% of the boiler’s design pressure or maximum allowable working pressure (MAWP).3 This 10% limit represents a critical safety buffer, preventing the boiler from being subjected to pressures that could compromise its structural integrity. By rigorously verifying the safety valve system’s ability to effectively manage maximum steam generation, the APT directly contributes to the prevention of dangerous overpressure conditions. Uncontrolled pressure escalation is a leading cause of boiler damage, rupture, and catastrophic explosions.1
The purpose of the APT is explicitly stated as checking the “capacity of the safety valve” and its “suitability for this boiler”.3 This goes beyond merely verifying that a valve opens at its set pressure, which is a calibration function. It is fundamentally about the valve’s ability to discharge a sufficient volume of steam to limit pressure rise. A valve might be perfectly calibrated to open at the correct pressure, but if its flow capacity is inadequate for the boiler’s maximum steam generation rate, it will fail the accumulation test. This highlights a critical distinction between a static, set-point characteristic of a valve and its dynamic, flow-based performance requirement when integrated into a boiler system. This emphasizes that boiler safety valves are not passive pressure switches but active flow control devices. Their selection, sizing, and verification must consider the boiler’s maximum energy output and steam generation rate, not just its operating pressure. This underscores the complexity of pressure relief system design and the necessity of system-level testing to ensure that theoretical design matches real-world operational performance.
Key Parameters and Requirements
The APT involves several critical parameters and requirements that must be strictly adhered to:
- Maximum Pressure Limit: The accumulated pressure observed during the test must not, under any circumstances, exceed 10% of the boiler’s design pressure.3
- Test Duration: The duration of the test is dependent on the boiler type:
- For fire-tube boilers: The test must be sustained for 15 minutes.3
- For water-tube boilers: The test must be sustained for 7 minutes.3
- Firing Conditions: The boiler must be maintained under full firing conditions throughout the entire duration of the test.3
- Feedwater Management: Feedwater supply should be strictly limited to only what is necessary to maintain a safe working water level within the boiler, preventing both low-water conditions and excessive water carryover.3
- Main Steam Stop Valve Position: The boiler’s main steam stop valve must be fully closed before and during the test.3
3. Accumulation Pressure Test vs. Safety Valve Setting (Pop Test)
Distinguishing Objectives and Methodologies
Understanding the distinct objectives and methodologies of the Accumulation Pressure Test (APT) and safety valve setting (often referred to as a “pop test” or calibration) is crucial for comprehensive boiler safety. While both are essential for pressure integrity, they serve different purposes and are conducted under different conditions.
Safety Valve Setting (Pop Test/Calibration)
The primary objective of a safety valve setting is to precisely verify and adjust the specific pressure at which an individual safety valve begins to open (its “set pressure” or “popping point”) and the pressure at which it fully closes (its “reseating pressure” or “blowdown”).7 This is fundamentally a calibration procedure for the valve itself.
This test is typically performed off-boiler, on a dedicated test bench, utilizing a controlled external pressure source such as compressed air or nitrogen.7 During the test, the inlet pressure to the valve is slowly and incrementally increased until the valve audibly “pops” or lifts. At this precise moment, the pressure reading is recorded as the set pressure. Further, the pressure at which the valve achieves full opening (overpressure) and the pressure at which it fully closes and seals (reseating pressure) are also noted.7 Any necessary adjustments to the set pressure are made by altering the compression of the valve’s internal spring.7 Key parameters observed include the set pressure (with a typical tolerance of ±3% of the set pressure 8), the overpressure (the pressure above set pressure required for full valve opening, typically up to 10% above set pressure 7), and the blowdown or reseating pressure (the pressure at which the valve fully closes, which for valves set at 375 psi or greater, should not be lower than 96% of their set pressure, with specific limits for lower pressures 9).
Accumulation Pressure Test (APT)
In contrast, the APT’s objective is to verify the total combined relieving capacity of all safety valves installed on a boiler. The goal is to ensure that this collective capacity is sufficient to prevent the boiler’s internal pressure from accumulating beyond a safe limit—specifically, 10% of its design or maximum allowable working pressure (MAWP)—under conditions of maximum heat input and no steam demand.3 This is an on-boiler, system-level performance test.
The APT is conducted on the operational boiler itself. The procedure involves closing the main steam stop valve and maintaining the boiler under full firing conditions.3 The boiler pressure is then allowed to rise naturally until the safety valves lift and begin discharging steam. The maximum pressure reached during a specified test duration (15 minutes for fire-tube boilers or 7 minutes for water-tube boilers) is carefully observed and recorded.3 The critical parameters for the APT are the maximum pressure accumulation (which must not exceed 10% of the boiler’s design pressure 3) and the specific test duration, which varies by boiler type.3
Interrelationship and Complementary Roles in Boiler Safety
While the pop test and the APT are distinct in their objectives and methodologies, they are fundamentally complementary and interdependent in ensuring comprehensive boiler safety. A striking difference lies in the nature of the testing: the pop test is an off-boiler, bench-based calibration, implying a static and controlled environment, whereas the APT is performed on the operational boiler under full firing conditions with the main stop valve closed. This highlights a crucial distinction: the pop test verifies a component’s isolated functional characteristic (its set point), whereas the APT validates the system’s integrated performance under realistic, dynamic operational stress. The dynamic nature of the APT, involving steam generation and flow, is far more complex than simply applying static pressure. This underscores that laboratory or bench tests, while indispensable for initial calibration and component verification, are inherently insufficient for comprehensive safety assurance in complex, dynamic systems like boilers. Real-world operational variables, such as the boiler’s actual steam generation rate, system volume, and thermal dynamics, can only be accurately assessed through integrated, full-scale system tests like the APT. This reinforces the need for a multi-tiered testing approach in critical safety applications.
The safety valve setting ensures that the first layer of defense (individual valve opening) operates correctly at the design pressure. The APT then verifies the second, overarching layer of defense – that the collective discharge capacity of all these valves is sufficient to prevent catastrophic overpressure, even when the boiler is producing its maximum steam output with no demand. This deliberate layering of safety checks, from precise individual component calibration to rigorous system-level performance validation, reveals a robust, multi-layered approach to risk mitigation in boiler operation. It implies that safety is not reliant on a single point of failure prevention but on ensuring redundancy and adequate capacity across multiple critical junctures. This layered approach is a hallmark of high-reliability engineering and safety management. It signifies that robust safety in industrial systems is achieved not by a single control, but by a hierarchy of controls and redundant systems. The APT, in this context, acts as the ultimate validation of this layered safety architecture, confirming that the entire pressure relief system can handle the boiler’s full energy potential.
Table 1: Comparison of Accumulation Pressure Test and Safety Valve Setting (Pop Test)
Feature | Accumulation Pressure Test (APT) | Safety Valve Setting (Pop Test/Calibration) |
Objective | Verify total combined relieving capacity of all safety valves. | Verify individual valve’s opening (set) and closing (reseating) pressures. |
Location of Test | On-boiler, under operational conditions. | Off-boiler, on a dedicated test bench. |
Test Medium | Boiler steam. | Compressed air or nitrogen. |
Primary Measurement | Maximum accumulated pressure. | Set pressure, overpressure, and reseating pressure. |
Key Parameter Verified | System’s capacity to prevent overpressure under full load. | Individual valve’s set point and blowdown. |
Maximum Pressure Limit | Not to exceed 10% of boiler’s design/MAWP. | Set pressure tolerance (e.g., ±3%), overpressure (e.g., up to 10% above set pressure). |
When Performed | For new boilers, new/overhauled safety valves, and periodically as per regulations. | During manufacturing, after repair/overhaul, and for periodic calibration. |
4. Detailed Procedure for Conducting an Accumulation Pressure Test
Conducting an Accumulation Pressure Test is a high-stakes operation that demands meticulous planning, rigorous safety protocols, and precise execution.
General Considerations and Safety Protocols (Pre-Test Preparations)
The accumulation pressure test is a high-risk operation and must only be conducted by highly trained, competent, and authorized personnel who are thoroughly familiar with boiler operation, safety valve mechanics, and emergency procedures.7 Prior to commencing the test, the entire test area must be clearly demarcated and isolated using appropriate barriers, such as red danger tape. Prominent warning signs must be posted to deter non-essential personnel and ensure they maintain a safe distance from the boiler.10
All personnel involved in or present near the test area must wear the required Personal Protective Equipment (PPE). This typically includes, but is not limited to, hardhats, safety glasses, and gloves. Depending on the specific risks, additional PPE such as face shields and hearing protection may also be mandatory.7 A comprehensive emergency response plan, specifically tailored for boiler overpressure incidents, must be established, communicated, and understood by all affected workers. This plan should detail emergency shutdown procedures and provide readily accessible emergency contact information.10
All test equipment, particularly pressure gauges, must be securely connected to the system.10 It is imperative to use properly calibrated pressure gauges. Ideally, two gauges should be utilized: one positioned at the pressure source and another at the highest or furthest point from the source to ensure accurate and consistent readings. Before installation, these gauges must be checked to ensure they register zero; if not, they should be immediately replaced.10 The maximum working pressure (MAWP) of the boiler should be clearly marked with a red line or dot on the pressure gauge.12 The specific test pressure and the boiler’s design pressure must be verified with the system engineer or another qualified authority.10
A thorough walk-down inspection of the boiler system is essential. All joints and connections must be exposed for visual inspection; this may necessitate the removal of insulation.10 Inspect for any damaged components, misaligned segments, or other anomalies that could compromise the test’s safety or validity.10 Any parts of the system that are not intended to be part of the accumulation test must be properly isolated to prevent unintended pressurization.10 All necessary lockout/tagout (LOTO) procedures must be completed to ensure energy sources are controlled and equipment cannot be inadvertently activated.10 A dedicated, open drain pipe must be fitted to the lowest part of the safety valve chest on the discharge side of the valves. This pipe must be led clear of the boiler and must not have any valve or cock fitted throughout its length, ensuring unimpeded discharge.6
The extensive emphasis on pre-test safety measures—such as area isolation, mandatory PPE, emergency planning, and rigorous equipment checks (e.g., calibrated gauges registering zero)—is not merely a checklist formality. It reflects the profound inherent danger of a test that deliberately pushes a pressure vessel to its operational safety limits. The meticulousness required for gauge calibration and leak detection before pressurization directly impacts the accuracy and integrity of the test results, which, in turn, directly correlates with the safety of personnel. A flawed pre-test setup can lead to misleading results or, worse, a catastrophic failure during the test itself. This highlights that safety in high-pressure industrial systems is not an operational add-on but an intrinsic part of the planning and preparation phase. It underscores the paramount importance of a robust safety culture, strict adherence to Standard Operating Procedures (SOPs), and comprehensive risk assessment to mitigate the severe hazards associated with such critical testing operations.
Execution Steps (On-Boiler Test)
The execution of the APT involves precise steps to simulate the “worst-case scenario” safely:
- Boiler Preparation: Ensure the boiler’s water level is at a safe working level, typically at the normal operating level. During the test, only the minimum amount of feedwater necessary to maintain this safe working water level should be supplied.3 The boiler’s main steam stop valve must be fully closed to prevent steam from exiting the boiler through normal operational pathways.3 The feedwater supply should be shut off 5, or strictly controlled to ensure only the necessary amount is supplied to maintain the safe water level.3 The boiler’s cut-off pressure should be increased, and any high-pressure cut-off interlocks should be bypassed to allow pressure to rise beyond normal operating limits for the test.3 The boiler’s firing rate must be set to its maximum capacity to ensure full steam generation.5
- Pressure Accumulation and Valve Activation: As the boiler continues to fire at maximum capacity with no steam outlet, the internal pressure will steadily rise. The safety valve(s) will then lift automatically as their set pressure is reached.3 Continuously monitor the pressure gauge. The critical observation is to ensure that the maximum accumulated pressure reached during the test does not exceed 10% of the boiler’s design pressure.3
- Test Duration: Maintain these conditions—full firing, closed main stop valve, and safety valves lifting—for the specified duration: 15 minutes for fire-tube boilers 3 and 7 minutes for water-tube boilers.3 The test duration is also contingent on maintaining a safe working water level throughout; the test is carried out for “as long as the water permits in the boiler”.5
The repeated mention of maintaining a “safe working water level” and conducting the test “as long as the water permits” 3 is critically important for both the safety and the validity of the APT. Low water levels during a high-firing test can lead to severe overheating, component damage (e.g., loosened/cracked tubes, melted metal), and potentially a catastrophic boiler explosion if water is suddenly introduced.2 Conversely, excessive water can lead to poor steam quality or carryover.15 Therefore, precise and continuous water level management is an often-underestimated, yet vital, aspect that directly influences the ability to safely complete the test for its required duration and obtain accurate results. This highlights the complex and dynamic interplay of various operational parameters during a high-stress test. It means that boiler operators and test personnel require a deep, integrated understanding of boiler dynamics beyond just pressure readings. They must recognize how seemingly auxiliary factors like water level directly influence the safety, integrity, and ultimate success of a primary safety verification test, reinforcing the need for holistic operational expertise.
Table 2: Accumulation Pressure Test Duration by Boiler Type
Boiler Type | Standard Test Duration |
Fire-Tube Boiler | 15 minutes |
Water-Tube Boiler | 7 minutes |
Post-Test Procedures and Documentation
Upon completion of the test, a structured approach is necessary to ensure safety and proper record-keeping:
- Safe Pressure Release: Following the completion of the test, the boiler pressure must be safely and gradually reduced according to established Standard Operating Procedures (SOPs).10 It is absolutely critical never to attempt to repair any leaks or perform maintenance while the system remains under pressure.10
- System Drainage: Once the pressure is safely relieved, the boiler system should be drained. If the test medium was water, any waste liquid must be collected and disposed of in accordance with facility and environmental regulations.10
- Thorough Inspection: A meticulous inspection of all boiler components, particularly all joints and connections, must be conducted to identify any signs of leakage or damage that may have occurred during the test.10
- Repairs and Retesting: Any leaks or defects discovered during the post-test inspection must be promptly and properly repaired. If significant repairs are made, or if the initial test results were unsatisfactory, the accumulation pressure test (or relevant sub-tests) must be re-performed to confirm the boiler’s integrity and compliance.10
- Comprehensive Documentation: All aspects of the test, including pre-test checks, observed pressures, durations, any anomalies, and all post-test repairs, must be meticulously documented in a dedicated boiler house log book. This record-keeping is essential for regulatory compliance, maintenance history, and future operational planning.12 The test results must be verified and certified by the authorized inspection official.
5. Regulatory Frameworks and Compliance
Importance of Compliance
The operation of boilers is subject to rigorous regulatory oversight due to the inherent and significant risks associated with high-pressure and high-temperature systems. Strict adherence to national and international codes and standards is not merely a recommendation but a mandatory requirement for the design, construction, installation, inspection, and ongoing testing of boilers, including the critical Accumulation Pressure Test.17 Non-compliance can lead to severe penalties, operational shutdowns, and legal liabilities.
ASME Boiler and Pressure Vessel Code (BPVC) Requirements
The ASME BPVC is a globally recognized and comprehensive set of standards that governs the design, fabrication, and inspection of boilers and pressure vessels. It is continuously updated by leading industry experts to reflect evolving technology and safety practices.17 Section I of the BPVC, specifically, outlines the “Rules for Construction of Power Boilers”.22
PG-67 (Overpressure Protection Requirements)
This section details the fundamental requirements for pressure relief devices. Safety valves must be set at or below the maximum allowable working pressure (MAWP) of the boiler. If multiple valves are used, the highest pressure setting is permitted to exceed the MAWP by no more than 3%.9 The total range of pressure settings for all saturated-steam safety valves on a single boiler must not exceed 10% of the highest pressure to which any valve is set.9 Crucially, the total combined relieving capacity of all pressure-relieving valves (including power-actuated valves) must be not less than 10% of the maximum design steaming capacity of the boiler under any operating condition, as determined by the manufacturer.9 During an accumulation test, the boiler pressure shall not rise more than 10% above the MAWP.9
PG-72 (Operation of Pressure Relief Valves)
This section addresses the operational characteristics of safety valves. Safety valves must be designed and constructed to operate smoothly, without “chattering” (rapid opening and closing), and must attain their full lift at a pressure no greater than 3% above their set pressure.9 The “blowdown” (the pressure differential between the popping point and the reseating point) must not exceed 4% of the set pressure, or specific psi values depending on the set pressure range.9 The spring in a safety valve should not be reset for any pressure more than 5% above or below its marked pressure, unless the new setting falls within the manufacturer’s established spring design range or is otherwise deemed acceptable by the manufacturer.9
PG-73 (Minimum Requirements for Safety and Safety Relief Valves)
This section outlines specific design and testing criteria for the valves themselves.
- Mechanical Requirements: Valves must incorporate robust guiding arrangements to ensure consistent operation and tightness. Key components like the seat must be securely fastened to the valve body to prevent lifting, and a body drain below seat level is required and must not be plugged.9
- Material Requirements: Cast iron seats and disks are explicitly prohibited. All adjacent sliding surfaces (e.g., guides and disks) and springs must be made of corrosion-resistant material or have a corrosion-resistant coating.9
- Manufacturer/Assembler Testing: Valves exceeding 1 inch (DN 25) inlet size or 300 psig (2070 kPa) set pressure must undergo pressure testing of primary pressure-containing cast and welded parts at 1.5 times their design pressure after all machining operations are complete, with no visible signs of leakage.9
- Capacity Certification: Capacity certification tests are required to be conducted using dry saturated steam, adhering to specific quality (minimum 98%) and superheat (maximum 20°F) limits.9
- Failure Protocol: If any valve fails to relieve at or above its certified capacity or does not meet performance requirements, additional replacement valves must be tested.9
Indian Boiler Regulations (IBR) 1950 Specifics
The Indian Boiler Regulations (IBR) 1950 constitute a comprehensive set of mandatory standards governing the materials, design, construction, inspection, and testing of boilers and boiler components for use in India.19 Compliance with IBR is strictly enforced by the Indian government, and imported equipment must be accompanied by a certificate confirming IBR compliance, endorsed by a designated Inspecting Authority.19 The Central Boilers Board is responsible for regularly reviewing and updating these regulations to align with advancements in boiler technology.19
Accumulation Test Requirements
Consistent with international best practices, IBR mandates that during an accumulation pressure test, the pressure must not exceed 10% of the boiler’s working pressure.3 The specified durations for the accumulation test under IBR are 15 minutes for fire-tube (also referred to as cylindrical or smoke tube) boilers 3 and 7 minutes for water-tube boilers.3 Safety valves are required to be set to lift at a pressure not greater than 3% above the approved working pressure (design pressure).13
IBR 1950 also provides extensive technical guidance on material specifications, welding and jointing procedures, thickness calculations for pressure vessels and tubes, design of fittings, and detailed inspection guidelines.21 Article 391A (b) of IBR 1950 makes it mandatory to assess boiler components through non-destructive and destructive testing for boilers operating at 400℃ and above (creep range). For boilers operating below 400℃, remnant life assessment is required after 25 years of operation.25
A striking observation is the consistent 10% accumulation limit specified by both ASME 9 and IBR.3 This indicates a global consensus on this critical safety margin, reflecting a shared understanding of the engineering principles required for overpressure protection. However, the IBR frequently refers to “classification society requirement” 3 and highlights its “strictly enforced” nature for imports 19, suggesting a more prescriptive, national regulatory framework compared to ASME’s broader “code” status. Furthermore, IBR’s detailed regulations on material testing, welder certification, and remnant life assessment 21 demonstrate a deeper and more explicit regulatory focus on the long-term integrity and lifecycle management of boilers within its jurisdiction. This reveals that while fundamental safety engineering principles (like the 10% overpressure limit) are often harmonized globally, the implementation and enforcement of these principles can vary significantly across national regulatory bodies. This necessitates that global manufacturers and operators develop a sophisticated understanding of both universal standards and specific national requirements, requiring specialized compliance expertise and potentially different operational protocols depending on the jurisdiction.
The ASME BPVC (PG-67, PG-72, PG-73) and IBR 1950 21 detail requirements that extend far beyond just the operational test of safety valves. They cover material specifications, design parameters, manufacturing processes (e.g., testing of parts at 1.5 times design pressure 9), welding procedures, and even long-term integrity assessments like remnant life assessment.25 This comprehensive scope indicates that the accumulation pressure test is not a standalone check, but rather the culmination and ultimate validation of adherence to a long chain of compliance requirements that begin at the very inception of a boiler’s life (design and material selection) and continue through its manufacturing, installation, and operational lifespan. A failure in the APT could therefore signal underlying deficiencies at any of these preceding stages, not just a malfunctioning valve. This emphasizes that boiler safety is a continuous, lifecycle concern, not merely an operational one. Regulatory bodies ensure safety by imposing stringent requirements at every stage of a boiler’s existence—from its initial design and material selection, through its manufacturing and assembly, to its commissioning, operation, and eventual end-of-life assessment. This holistic regulatory view is crucial for preventing systemic failures and ensuring sustained safety and reliability throughout the boiler’s service life.
Table 3: Key Regulatory Requirements for APT (ASME vs. IBR)
Regulatory Aspect | ASME BPVC Section I | Indian Boiler Regulations 1950 (IBR) |
Governing Body/Authority | ASME (American Society of Mechanical Engineers) | Central Boilers Board (Indian Government) |
Primary Code/Regulation Document | ASME Boiler and Pressure Vessel Code Section I (PG-67, PG-72, PG-73) | Indian Boiler Regulations 1950 |
Maximum Allowable Accumulation Pressure | Not to exceed 10% of Maximum Allowable Working Pressure (MAWP) 9 | Not to exceed 10% of Working Pressure 3 |
Fire-Tube Boiler Test Duration | Not explicitly stated for APT duration in provided snippets, but general boiler rules apply. | 15 minutes 3 |
Water-Tube Boiler Test Duration | Not explicitly stated for APT duration in provided snippets. | 7 minutes 3 |
Safety Valve Set Pressure Tolerance | Highest set pressure not > 3% above MAWP 9 | Not > 3% above approved working pressure 13 |
Scope of Regulatory Coverage | Comprehensive for power boilers (design, construction, operation, maintenance of pressure relief devices). | Comprehensive for boilers in India (materials, design, construction, inspection, testing, and lifecycle management). |
6. Safety Implications, Common Issues, and Best Practices
Risks and Consequences of Improper or Omitted APT
The risks associated with an improper or omitted Accumulation Pressure Test are severe and can lead to catastrophic outcomes.
- Catastrophic Boiler Explosion or Rupture: This is the most severe and devastating consequence. If the safety valves fail to adequately relieve pressure during an overpressure event (which the APT is designed to simulate and prevent), the internal pressure can rise unchecked, leading to a violent rupture of the boiler vessel. Such events cause immense property damage, severe injuries, and often fatalities.1
- Severe Component Damage and Structural Integrity Compromise: Even without a full explosion, excessive pressure puts immense, undue strain on all boiler components. This leads to accelerated wear and tear, material fatigue, and the development of cracks and leaks in critical pressure boundaries.1 Specific damages can include loosened or cracked tubes, melted metal, and compromised seals.1 Over time, this stress weakens the boiler’s structural integrity, making it more susceptible to future failures.
- Operational Inefficiency and Increased Costs: A boiler operating under conditions where its safety valves are inadequate or malfunctioning will inherently operate inefficiently. This can lead to increased energy consumption and higher utility bills.1 Furthermore, the long-term implications include a significantly reduced boiler lifespan and increased maintenance costs due to more frequent repairs and component replacements necessitated by high-pressure-induced stress.1
- Regulatory Non-Compliance and Legal Ramifications: Failure to properly perform the accumulation pressure test, or a failure to pass it, constitutes a serious breach of regulatory requirements (e.g., ASME, IBR). This can result in severe penalties, including substantial fines, mandatory operational shutdowns, and significant legal liabilities for the operating entity and responsible personnel (implied by the strict enforcement of IBR 19).
- Underlying Causes of Failure: The failure of an APT, or a safety valve malfunction in general, can stem from various issues, including: inherently malfunctioning pressure relief valves (e.g., failure to open, chattering, restricted lift), improper sizing or selection of the safety valve for the boiler’s capacity, inadequate or neglected maintenance, or critical human error during operation or testing.1
Common Problems Encountered During APT and Troubleshooting
Several common problems can arise during an APT, often indicating deeper issues within the boiler system.
Safety Valve Malfunction
- Failure to Lift or Open: A primary concern is when a safety valve fails to open at its set pressure or lift sufficiently. Common causes include the accumulation of dirt or debris, corrosion on internal components, mechanical wear of moving parts, or incorrect sizing/selection of the valve for the boiler’s capacity.26 Improper installation and a lack of regular, proactive maintenance are identified as primary contributors to these issues.26
- Chattering or Fluttering: This undesirable phenomenon involves the rapid, uncontrolled opening and closing of the safety valve disk. It is often indicative of issues beyond just the valve itself, such as improper blowdown adjustment, inadequate inlet piping design (leading to pressure drop), or an insufficient accumulation vessel size.27 Chattering can cause significant damage to the valve’s internal components and lead to premature wear.9
- Leakage or Simmering: This occurs when a safety valve does not fully close and seal after discharging, leading to a continuous, small release of steam. Causes include worn seals, foreign matter lodged on the valve seat, or improper spring adjustment.26
- Restricted Lift: If the valve does not open to its full design lift, its relieving capacity is significantly reduced. This can be caused by an incorrect spring, worn or galled guiding surfaces that impede movement, or improper assembly of the valve’s internal components.27
Boiler Water Quality Issues
Poor water chemistry can severely impact boiler performance and safety, including during an APT.
- Scale Buildup: Minerals present in the boiler water can form hard scale deposits on internal surfaces. These deposits act as insulation, blocking steam flow, significantly reducing heat transfer efficiency, and potentially causing localized overheating and corrosion of boiler tubes.29 Scale can also encrust and damage water and safety probes, leading to inaccurate readings or automatic shutdowns.30
- Sludge Deposits: These are accumulations of softer solids that precipitate in the boiler water. If not properly managed, sludge can become dense and tenacious, especially when exposed to high heat or low water levels (e.g., during draining), forming a baked-on layer. This restricts water flow, increases temperatures, and can damage boiler components, similar to scale.29
- Corrosion: The deterioration of boiler metals due to chemical reactions, primarily oxidation. Common causes include excessive dissolved oxygen, acidic water (low pH), or caustic corrosion (high pH). Corrosion manifests as pitting, rust, and leaks, compromising the boiler’s structural integrity.13
- Foaming: This occurs when solids detach from boiler surfaces and float to the top, causing the water to foam as it heats and generates steam.30 Foaming can lead to water carryover into the steam system, affecting steam quality and downstream equipment.
Operational Issues
- Low Water Levels: An extremely dangerous condition where the water level inside the boiler falls below safe operating thresholds. This leads to rapid overheating of metal surfaces, causing warping, cracking, or failure of components. If water is suddenly added to an overheated boiler, it can instantly flash into steam, generating tremendous pressure and potentially leading to a catastrophic explosion.2
- Improper Firing or Combustion: Issues with fuel supply, air-to-fuel ratio, or burner maintenance can lead to incomplete combustion, resulting in soot buildup, reduced efficiency, flare-backs, or even fireside explosions within the furnace.13
While the primary function of the APT is to verify safety valve capacity, a failure during the test (e.g., exceeding the 10% accumulation limit, or valve chattering) rarely points to an isolated valve defect. Instead, it often serves as a critical diagnostic indicator of deeper, systemic problems within the boiler system. For instance, if pressure accumulation is too high, it might not just be a faulty valve, but an undersized valve for the boiler’s actual steam generation rate, or underlying boiler water quality issues (like scale or sludge buildup 29) that impede heat transfer, leading to higher-than-anticipated steam production that overwhelms the valve’s capacity. Similarly, chattering 27 suggests dynamic instabilities in the system beyond the valve itself. This implies that the APT is not merely a pass/fail compliance check; its specific failure modes provide invaluable diagnostic information that can trigger investigations into design adequacy, operational practices, and the overall effectiveness of maintenance programs, leading to holistic system improvements rather than superficial fixes. This reframes the APT as a high-level performance audit for the entire boiler-safety valve integrated system. The results of this test can serve as a crucial trigger for root cause analysis, prompting a re-evaluation of design specifications, operational parameters, and maintenance strategies. This elevates the APT from a routine test to a vital component of a continuous improvement cycle for boiler safety and reliability.
Overall Boiler Safety Best Practices and Maintenance
To ensure the sustained safe and efficient operation of boilers, a holistic approach to safety and maintenance is indispensable:
- Regular and Thorough Inspections: Implement a rigorous schedule for routine boiler inspections. These checks should identify potential issues such as leaks, corrosion, cracks in the boiler body, and verify the proper functioning of pressure gauges, safety valves, and water level indicators.15
- Proactive Water Level Management: Operators must diligently monitor and maintain proper water levels daily using the gauge glass. Ensure feedwater pumps are operational and that low-water cutoff devices are functional to prevent dry firing.14 Conduct weekly full functional tests of low-water level alarm systems.16
- Safety Valve Testing and Maintenance Program: Safety valves should be tested frequently to ensure they open at the correct pressure.15 A proactive maintenance approach is crucial, involving routine inspection, testing, and timely replacement of worn components. Proper sizing and selection of safety valves based on the boiler’s specific requirements are equally critical for reliable operation.26
- Comprehensive Water Treatment Program: Implement and strictly adhere to a robust water treatment program to prevent the formation of scale, sludge, and corrosion within the boiler system.13 Regularly test boiler water for key parameters such as pH balance, dissolved solids, and contaminants.13 Perform periodic boiler blowdowns to remove sludge and impurities.13
- Adherence to Startup and Shutdown Procedures: Operators must strictly follow manufacturer guidelines for boiler startup and shutdown to prevent thermal shock, pressure surges, and component damage.15
- Optimal Ventilation and Combustion Control: Ensure adequate ventilation in boiler rooms to allow for proper expulsion of flue gases and prevent carbon monoxide buildup. Regularly adjust the air-to-fuel ratio for complete and efficient combustion.15
- Continuous Operator Training: Provide comprehensive and ongoing training for boiler operators on correct procedures for maintaining boiler pressure, recognizing signs of issues, and appropriate emergency responses.14
- Strict Preventative Maintenance Schedule: Implement and adhere to a rigorous preventative maintenance schedule that includes lubricating moving parts, inspecting seals, cleaning boiler tubes and combustion chambers, and checking electrical connections and wiring.15
The research consistently emphasizes the impact of “operator error” 2, the necessity of “proper startup and shutdown procedures” 15, the importance of “operator training” 14, and the adherence to a “strict maintenance schedule”.15 Furthermore, the detailed pre-test safety protocols 10 highlight the meticulous human involvement required for safe execution. This consistent focus on human actions and procedural adherence indicates that even a perfectly designed and mechanically sound boiler system, equipped with fully functional safety devices, can still lead to catastrophic failure if operated or maintained improperly. The human element, through training, discipline, and a strong safety culture, is therefore as critical, if not more so, than the mechanical integrity of the equipment. This moves beyond a purely technical discussion of boiler components to acknowledge that boiler safety is fundamentally a socio-technical system. While robust engineering design and component reliability form the foundation, the ultimate safety performance is heavily dependent on the human element – the competence, vigilance, and adherence to established procedures by operators and maintenance personnel. This underscores the need for continuous training, a strong safety culture, and effective human-machine interfaces to prevent accidents and ensure the long-term integrity and safe operation of boiler assets.
7. Conclusion
The Accumulation Pressure Test stands as a cornerstone of boiler safety, playing a unique and indispensable role in empirically verifying the critical function of pressure relief systems. Unlike routine safety valve setting, which focuses on the precise calibration of individual components, the APT provides comprehensive, system-level performance validation. It rigorously tests the collective capacity of all safety valves to manage the boiler’s maximum steam generation under no-demand conditions, ensuring that internal pressure remains within safe limits.
The imperative for boiler safety demands strict adherence to established regulatory requirements, such as those outlined by the ASME Boiler and Pressure Vessel Code and the Indian Boiler Regulations 1950. These frameworks, while sharing fundamental safety principles like the 10% accumulation limit, also present specific jurisdictional requirements that necessitate detailed understanding and compliance. The meticulous execution of the APT’s detailed procedural steps, underscored by comprehensive pre-test safety protocols, is paramount. Failures during this test are not merely isolated incidents but often serve as crucial diagnostic indicators of deeper, systemic issues within the boiler’s design, operation, or maintenance.
Ultimately, a robust and proactive approach to boiler safety is absolutely essential. This encompasses diligent and regular testing, including the Accumulation Pressure Test, coupled with comprehensive preventative maintenance programs, continuous operator training, and the cultivation of a strong safety culture. This holistic approach is vital for preventing catastrophic failures, ensuring sustained operational efficiency, extending the economic lifespan of boiler assets, and safeguarding both personnel and property.
Works cited
- Excessive Boiler Pressure Risks and Solutions: What to Know – Red River, accessed July 1, 2025, https://www.redriver.team/what-happens-if-theres-too-much-pressure-inside-the-boiler-unraveling-the-risks-and-solutions/
- Boiler Explosions Lawyer – Joe I. Zaid & Associates, accessed July 1, 2025, https://joezaid.com/practice-areas/boiler-explosions/
- Boiler Accumalation Test | PDF | Technology & Engineering – Scribd, accessed July 1, 2025, https://www.scribd.com/document/727282160/Boiler-Accumalation-Test
- Accumulation test of the boiler – Wärtsilä, accessed July 1, 2025, https://www.wartsila.com/encyclopedia/term/accumulation-test-of-the-boiler
- SRV – Accumulation Test | PDF | Home & Garden | Technology …, accessed July 1, 2025, https://www.scribd.com/document/694314000/SRV-Accumulation-Test
- BOILER :- – Alfidelfi, accessed July 1, 2025, https://alfidelfi.com/class%202/1TRAN%20TO%20WEB/AMEN/141-BOILER.htm
- PSV testing procedure: Popping test methods and PSV calibration (with PDF), accessed July 1, 2025, https://www.allaboutpiping.com/psv-popping-test-procedure/
- A Simple Pressure Safety Valve Calibration Procedure, accessed July 1, 2025, https://calibrationawareness.com/a-simple-pressure-safety-valve-calibration-procedure
- ASME CODE – TUBACERO, accessed July 1, 2025, https://www.tubacero.com.uy/pdf/ASME%20Codes%20-%202nd%20Edition.pdf
- MCAA Guide to Pressure Testing Safety, accessed July 1, 2025, https://www.mcaa.org/pca/wp-content/uploads/sites/3/2016/03/SE86PDF.pdf
- The Hydro Test Procedure for Boilers – How Does It Work? – NiGen International, accessed July 1, 2025, https://nigen.com/boiler-hydro-test-procedure/
- New boiler testing rules | G Scale Central, accessed July 1, 2025, https://www.gscalecentral.net/threads/new-boiler-testing-rules.257708/
- Accumulation Pressure Test, Corrosion of Boilers on Ships, accessed July 1, 2025, https://marineengineeringonline.com/accumulation-pressure-test-corrosion-of-boilers-on-ships/
- Low Water Boiler Conditions: Avoiding Boiler Catastrophes – Rasmussen Mechanical Services, accessed July 1, 2025, https://www.rasmech.com/blog/low-water-boiler-conditions-avoiding-boiler-catastrophes/
- 10 Essential Boiler Safety Precautions Every Operator Should Follow – RIBO Industries, accessed July 1, 2025, https://ribo.in/10-essential-boiler-safety-precautions-every-operator-should-follow/
- Testing Requirements in the Boiler House – Spirax Sarco, accessed July 1, 2025, https://www.spiraxsarco.com/learn-about-steam/the-boiler-house/testing-requirements-in-the-boiler-house?sc_lang=en-GB
- ASME Boiler and Pressure Vessel Code (BPVC) – The American Society of Mechanical Engineers, accessed July 1, 2025, https://www.asme.org/codes-standards/bpvc-standards
- ASME Boiler and Pressure Vessel Code Evaluation and Equivalence Study for Liquefied Natural Gas Facilities – Regulations.gov, accessed July 1, 2025, https://downloads.regulations.gov/PHMSA-2018-0046-0006/attachment_3.pdf
- Indian Boiler Regulation (IBR) Inspections | TÜV SÜD – TUV Sud, accessed July 1, 2025, https://www.tuvsud.com/en-us/services/inspection/arise-inc/indian-boiler-regulation
- Indian Boiler Regulations (IBR) – Munich Re, accessed July 1, 2025, https://www.munichre.com/hsb/en/services/engineering/global-inspection/international-codes/indian-boiler-regulations-ibr.html
- Indian Boiler Regulations 1950 | PDF | Pipe (Fluid Conveyance) – Scribd, accessed July 1, 2025, https://www.scribd.com/doc/208146559/Indian-Boiler-Regulations-1950
- ASME BPVC Section I – Rules for Construction of Power Boilers | 2025 | Print Book, accessed July 1, 2025, https://www.asme.org/codes-standards/find-codes-standards/bpvc-i-bpvc-section-i-rules-construction-power-boilers
- Chapter Comm 41 (EXCERPTS FROM BOILER, PRESSURE VESSEL AND PIPING CODES AND STANDARDS) – Department of Safety and Professional Services, accessed July 1, 2025, https://dsps.wi.gov/Documents/Programs/MR/CodeArchives/2008Comm41Appedix.pdf
- Paper 1 – NPC, accessed July 1, 2025, https://npcindia.gov.in/NPC/User/Paper-1_2020.pdf
- Residual Life Assessments and Condition Monitoring – Boiler World Update, accessed July 1, 2025, https://boilerworldupdate.com/residual-life-assessments-and-condition-monitoring/
- Safety Valves Maintenance And Malfunction Reason – Nuova General Instruments, accessed July 1, 2025, https://www.nuovageneral.it/safety-valves-maintenance-and-malfunction-reason
- Typical Improper Repairs of Safety Valves, accessed July 1, 2025, https://www.nationalboard.org/index.aspx?pageID=164&ID=206
- Safety Valve Selection | Spirax Sarco, accessed July 1, 2025, https://www.spiraxsarco.com/learn-about-steam/safety-valves/safety-valve-selection?sc_lang=en-GB
- Chapter 12 Boiler Deposits: Occurence And Control – Veolia Water Technologies & Solutions, accessed July 1, 2025, https://www.watertechnologies.com/handbook/chapter-12-boiler-deposits-occurence-and-control
- Common Steam Boiler Problems & How to Troubleshoot Repairs – Chardon Labs, accessed July 1, 2025, https://www.chardonlabs.com/resources/common-steam-boiler-problems/
- Common Steam Boiler Issues and How to Fix Them – Hawleys, accessed July 1, 2025, https://www.hawleys.com.au/blog/our-blog/common-steam-boiler-issues/
- Boiler Risk Assessment | PDF – Scribd, accessed July 1, 2025, https://es.scribd.com/document/497196994/boiler-risk-assessment
- Boiler Safety Checklist, accessed July 1, 2025, https://www.canadasafetytraining.com/Safety_Blog/boiler-safety-checklist.aspx