BOILER WATER TREATMENT CHEMICALS AND ITS COMPOSITION
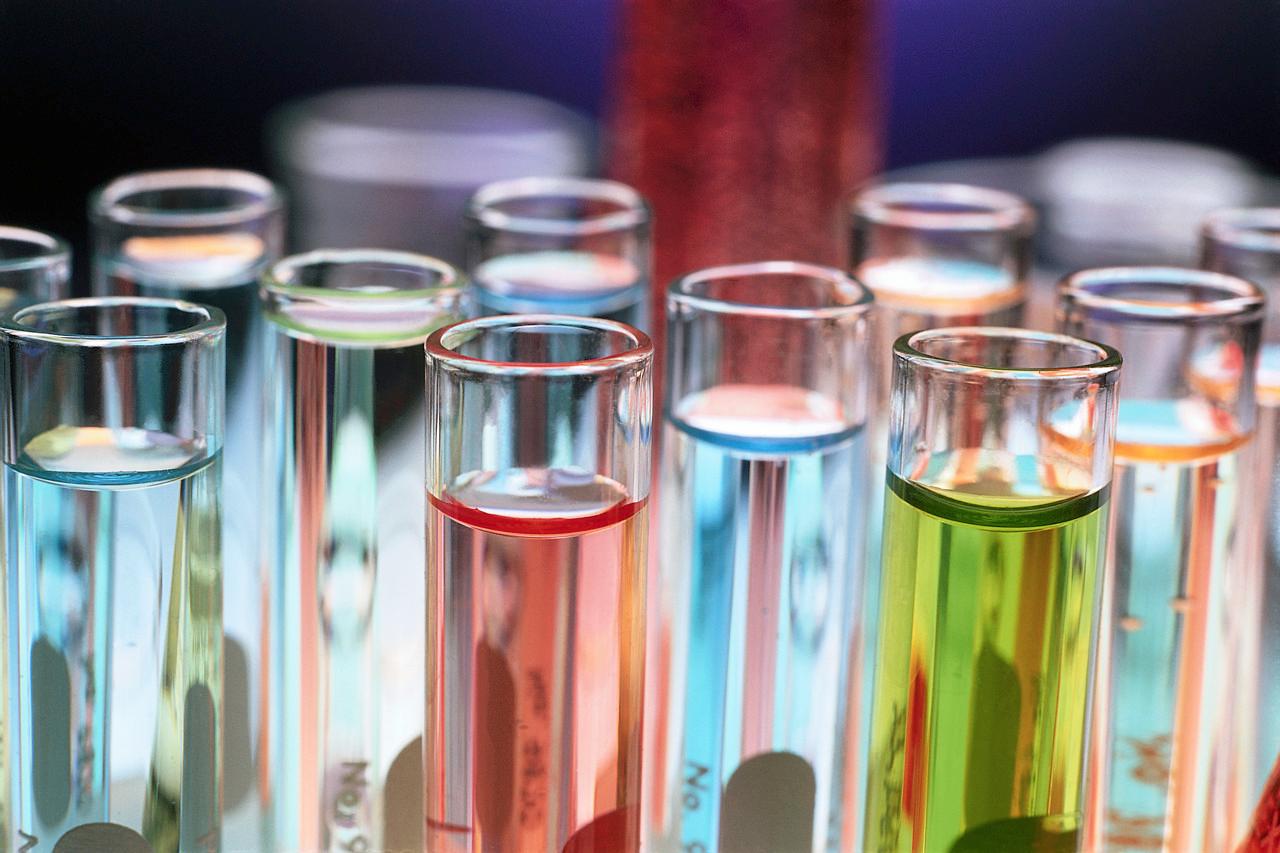
BOILER WATER TREATMENT CHEMICALS AND ITS COMPOSITION
IF YOU ARE INTERESTED IN BOILER WATER TREATMENTS & ITS PURPOSE READ THIS ARTICLE. CLICK HERE
Alkalinity
Treatment
For pressures below 20 bar dissolved O2 in the feed does not cause any serious problems so long as the water is kept alkaline
However cold feed should be avoided as this introduces large amounts of dissolved O2 are present, for pressures greater than 18.5 bar a dearator is recommended
Feed Treatment Chemicals
Sodium | Hydroxide |
Calcium | Bicarbonate (CaCO3 + Na2CO3) |
Magnesium | Bicarbonate |
Magnesium | Chloride. |
. | . |
Sodium | Phosphate |
Calcium | Carbonate |
Calcium | Sulphate |
Magnesium | Sulphate |
All in this column precipitated as hydroxide or phosphate based sludges | All in this column form sodium salts which remain in solution |
- Sodium Hydroxide
- Reacts with highly corrosive MgCl2
- Does not readily react with CaSO4
- Strongly alkaline
- Produces heat when mixed with water
- Absorbs CO2 changing to Sodium Carbonate
- Unsuitable for standard mixes
- Sodium Carbonate Na2CO3 ( soda ash )
- Alkaline
- At pressures above 14 bar some of the Sodium Carbonate decomposes to form NaOH and CO2 . Increasing on pressure increase
- Changes to Sodium Bi-Carbonate when exposed to air
- Still usable but larger amounts make control difficult
- Standard mix ingredient
- Sodium Hexa Meta Phosphate NaPO3 (calgon)
- Safe,soluble in water, slightly acidic
- May be injected any where as will only react in the boiler
- Suitable for LP blrs which require lower alkalinity
- DiSodium Phosphate Na2HPO4 (Cophos II)
- Neutral used with alkaline additive
- Combines with NaOH to give trisodium phosphate
- Basic constituent
- TriSodium Phosphate Na3 PO4 (Cophos III)
- Alkaline
- When added to water decomposes to NaOH and Na2 HPO4
- As water evaporated density increases and NaOH and Na2 HPO4 recombine
- Phosphates can form Phosphides which can coat metal to form a protective barrier, with excessive phosphate levels, this coating can be excessive on highly rated boilers operating at higher steaming rates
Chemicals are normally added as a dilute solution fed by a proportioning pump or by injection from pressure pot.
Use of chemicals should be kept to a minimum.
Injection over a long period is preferable as this prevents foaming.
Excessive use of phosphates without blowdown can produce deposits of phosphides on a par with scale formations.
Therefore it is necessary to add sludge conditioners particularly in the forms of polyelectrolytes, particularly in LP blrs
Oxygen Scavengers
- Hydrazine N 2 H 4
- Oxygen scavenger, continously injected to maintain a reserve within the boiler of 0.02 to 0.1 ppm and a feed water O2 content of less than 10 ppb
- At temperatures greater than 350oC , will decompose to ammonia and nitrogen and will aid in maintaining balanced alkalinity in steam piping.Steam volatile, neutralises CO2
- Inherent alkalinity helps maintain feed water alkalinity within parameters of 8.6 to 9.0.
- Used in boiler operating above 32 bar, will not readily react with O2 below 50oC hence risk of copper corrosion occurs with the ammonia stripping off the continuously reforming copper oxides.
- Supplied as a 35% solution
- Carbohydrazide (N 2 H3)2CO
- Is a combined form of Hydrazine
- It is superior to hydrazine in performace and is designed to minimise the vapours during handling
- Carbohydrazide and its reaction products create no dissolved solids
- Is an oxygen scavenger and metal passivator at both high (230’C) and low (65’C) temperatures
- Can be used with boilers up to 170 bar
- Diethylhydroxylamine DEHA
- Like hydrazine, provides a passive oxide film ( magnetite) on metal surfaces to minimise corrosion
- Contributes to pH netralisation to an extent that seperate condensate control may not be necessary
- Protects entire system-feedwater, boiler and condensate
- Sodium sulphite Na2SO3
- Takes the form of a soft white powder
- Slightly alkaline
- Will react with oxygen to form Sodium Sulphate at about 8ppm Sodium Sulphite to 1ppm Oxygen
- Use limited to low pressure boilers due to increasing TDS and reducing alkalinity by its action
- Tannins
- Certain alkaline tannin solutions have a good oxygen absorbing ability with about 6ppm tannin able to remove 1ppm oxygen.
- The reaction with oxygen is complex and unreliable, no official reserve levels exist for the maintenance of a system using tannin
- Erythorbic Acid (Sur-gard) R1-C(OH)
- An effective oxygen scavenger and metal passivator
- It is the only non-volatile scavenger which can be used with spray attemperation
- does not add measureable solids to the boiler water
- May be used in boilers up to 122 bar
- Officially recognised as a Safe Substance
- As with hydrazine a small amount of ammonia is created in the boiler, it is not recommended for layup.
Polymer Treatment
Polymer is a giant molecular built up by stringing together simple molecules
E.G.
Polyelectrolytes-Formed from natural or synthetic ionic monomers
Polyacrylates – Polymers of acrylic acid
Polyamides – Polymers of amides
Polymer treatment prevents scale formation and minimises sludge formation. It can also loosen scale so established blrs introduced to this form of treatment may develop leaks where previously plugged with scale. Especially in way of expanded joints. Also can absorb trace oil
Use limited to LP blrs as no PO4 present to prevent caustic alkalinity
For auxiliary blrs this is a superior form of treatment to the old alkaline and phosphate treatment. The correct level of alkalinity must be maintained as too low a level neutralises the electric charge of the polyelectrolyte. Too high causes caustic alkalinity.
Amine treatment
Compounds containing nitrogen and hydrogen.
Neutralising amines
Hydrazine N2H4
see above
Bramine ( cyclohexalamine )
(Bull & Roberts amine treatment)
Neutralising amine as with hydrazine. Used with hydrazine to maintain feed water alkalinity within parameters. As a knock on effect will slightly increase boiler water alkalinity.
Stable at high temperatures so is used more than hydrazine to control the steam line alkalinity as there is less chance of copper corrosion which occurs with the prescience of ammonia
Proper boiler water treatment eliminates sludge and scale deposits within the boiler. However, over along period of time a film of copper and iron oxides build up on the tube surface. Most of these oxides are transported from oxides of corrosion within the feed system to the boiler with the condensate.
Bramine reduces this corrosion and eliminates the build up of these oxide deposits.
Mechanism of function
Condensate from the condenser is very pure and slightly acidic, often referred to as ‘hungry water’. It can dissolve metals in trace amounts to satisfy this hunger.
Distilled make up water aggravates this situation containing much dissolved CO2 and hence being acidic carries its own corrosion products.
Trace amounts of bramine are introduced into the system to establish an alkalinity level greatly reducing the effects of the hungry water.
Some of the bramine is used almost immediately, most however, passes on to the boiler where it is then transported through boiler water, boiler stm drum, stm lines back to the condenser. It has no effect anywhere except the condensate system.
Bramine also has a cleaning effect and may assist in the cleaning the film off the tube over a period of time.
Bramine is safer to handle than Bramine and will protect all metals.
Hydrazine however readily breaks down to form ammonia which whilst protecting ferrous metals will attack those containing copper
Filming amines
Shows neutralising tendencies, main function however is to coat piping with a molecular water repellent protective film
Injection of amines
May be injected between HP and LP turbines in the X-over pipe or after the dearator.
Adding in X-over pipe-reduces corrosion of copper alloys
Dearator only effective as a feed heater
Adding after dearator -Dearator correctly performing as a dearator and feed heater. If possible the best system is to have a changeover to allow norm inj into the X-over at sea and injection after the dearator when the turbine shut down.
Limits of density/pressure
Sludge conditioning agents
- Coagulants-
- Mainly polyelectrolytes
- Prevents the precipitated sodium based particles forming soft scales
- Will keep oil in an emulsion
- the water must be kept alkaline
- Antifoams
- reduce the stability of water film around steam bubble and cause it to collapse.
- Common type polyamide is an organic compound of high molecular weight.
- In the event of severe contamination separate injection of an antifoam is recommended
- Dispersing agents
- Sludge conditioners such as starch or tannin.
- Prevent solid precipitates uniting to form sizeable crystals e.g. MgSO4
Treatment in boilers (non congruent)
LP tank blrs (<14 bar)
Na2CO3– precipitates salts, provides alkalinity
MgSO4– Sludge conditioners
Na2CO3 can break down to form NaOH in higher rated boilers hence initial dose with Na2SO4
Medium pressure tank blrs (<17.5 bar)
Na2CO3(3) + sodium phosphate(4) + sludge conditioners(1)
Medium to High pressure water tube <60 bar
Na2CO3 + Na2HPO4 +sludge conditioners
Oxygen scavengers also used to allow magnetite (Fe3O4) layer to form in the boiler
Boiler operating above 42 bar require a dearator.
HP to UHP blrs (42 to 80 bar)
Due to level of decomposition of Na2CO3 . NaOH preferred for better controllability Na2HPO4
NaOH attacks the magnetite layer. Congruent treatment used.
Permissible limits
Shell | WT | WT | WT | WT | WT | ||
TEST> | PPM | <17.5b | <17,5b | <32b | <42b | <60b | <85b |
Hardness | CaCO3 | <=5 | <=5 | <=5 | <=1 | <=1 | <=1 |
P.alk | CaCO3 | 150-300 | 150-300 | 150-300 | 100-150 | 50-100 | 50-80 |
T.D.S. | CaCO3 | <=7000 | <=1000 | <=1000 | <=500 | <=500 | <=300 |
Cl | CaCO3 | <=1000 | <=300 | <=150 | <=100 | <=50 | <=30 |
PO4 | PO4 | 30-70 | 30-70 | 30-70 | 30-50 | 30-50 | 20-30 |
N2H4 | N2H4 | — | — | — | 0.1 -1.0 | 0.1 – 1.0 | 0.1 – 1.0 |
SO3 | SO3 | 50-100 | 50-100 | 50-100 | 20-50 | — | — |
SiO2 | SiO2 | — | — | — | — | — | <=6.0 |
Fe | Fe | — | — | — | — | — | <=0.05 |
Cu | Cu | — | — | — | — | — | <=0.02 |
pH | pH | 10.5-11 | 10.5-11 | 10.5-11 | 10.5-11 | 10.5-11 | 10.3-11 |
Limits for feed water | |||||||
Cl | CL | <=10 | <=5 | <=1.0 | <=1.0 | <=1.0 | <=1.0 |
O2 | O2 | —- | —- | <=0.006 | <=0.003 | <=0.015 | <=0.01 |
NH3 | NH3 | —- | —- | —- | —– | —– | <=0.5 |
Fe | Fe | —- | —- | —- | —– | <=0.01 | <=0.01 |
Cu | Cu | —- | —- | —- | —– | <=0.01 | <=0.01 |
pH | pH | —- | —- | —- | 8.5-9.2 | 8.5-9.2 | 8.5-9.2 |
Good work, Very well explained.
For Hard Scale in Boiler which is the best polymer antiscalent please tell sir
thanks for writing a detailed article about boiler chemicals!
I want a engineering of boiler water treatment chemical contact 6361242499
If I Wanna increase my alkalinity do I increase the caustic amount
Yes, that is correct!
Anything toxic in storage containers?
You may have to refer to each chemical MSDS, Material safety data sheet. Usually, I have seen corrosive but not as Toxic! It cant be toxic due to maritime regulations.
Amines have two major advantages over ammonia. One is their higher basicity, which produces a greater rise in the pH of condensate per ppm of compound . The other is their higher relative volatility (RV), defined as the ratio of the amount of the substance (ammonia or amine) in condensate vapor to its amount in liquid-phase water at a given temperature and pressure. The higher the RV, the higher the percentage of the compound in the vapor phase. The lower the RV, the more quickly the amine falls out of solution and back into the condensate. As condensate forms at higher temperatures, a high-volatility amine stays in the vapor.
Cyclohexylamine supplier:luwenyu@eschemy.com
What’s chemical formula formation of Coagulant treatment for boiler test.
What is use of Sodium Aluminate 40℅ liquid in Boiler treatment and RO treatment chemicals
Sir pls lp boilers chemicals make ratio
How can calculate dosage of tannin based chemicals to boiler , please suggest
Also suggest any pdf or xls sheet for all chemical calculations to boiler LP MP AND HP on smane7030@gmail.com
Thank you
I would like to converse with your technical executive